Douai este un oraș situat în nordul Franței, la 200 de kilometri de Paris și 140 de kilometri de Bruxelles. Cunoscut în epoca medievală pentru o piață înfloritoare de materiale textile, orașul a fost cucerit de Ludovic al XIV-lea în 1667, distrus de armată britanică în 1712 și ocupat de armata germană pentru o bună parte din primul Război Mondial.
Începând din 1970, Douai găzduiește una dintre uzinele Grupului Renault, iar în cei peste 50 de ani de existență aici s-au produs peste 10 milioane de vehicule. Uzina de la Douai a căpătat o importanță strategică pentru francezi în 2018, atunci când Renault a anunțat că aici urma să fie produsă compacta electrică Megane E-Tech pe noua platformă modulară CMF-EV, dezvoltată special pentru producția de vehicule electrice.
Dar ăsta avea să fie doar începutul.
Într-un interval de numai 5 ani, Renault este acum pe punctul să finalizeze tranziția de la o uzină construită în 1970 pentru a produce mașini cu motoare termice la o uzină care produce exclusiv mașini electrice.
Printre altele, tranziția a venit și ca o reacție la reconfigurarea gamei de modele. De exemplu, până de curând aici s-a produs Renault Talisman, un model care a fost eliminat din gamă, în timp ce producția lui Renault Espace a fost deja mutată la uzina din Palencia (Spania) după lansarea noii generații în luna martie. Între timp, producția actualului Renault Scenic se încheie chiar în luna aprilie pentru a face loc viitoarei sale versiuni electrice, care nu a fost încă prezentată oficial.
Cu alte cuvinte, Renault Megane E-Tech este acum vedeta incontestabilă de la Douai, care acoperă aproximativ două treimi din producția totală actuală a uzinei. Acesta este contextul în care am vizitat recent uzina de la Douai, pentru a înțelege mai bine modul în care are loc această tranziție spre producția integrală de vehicule electrice.
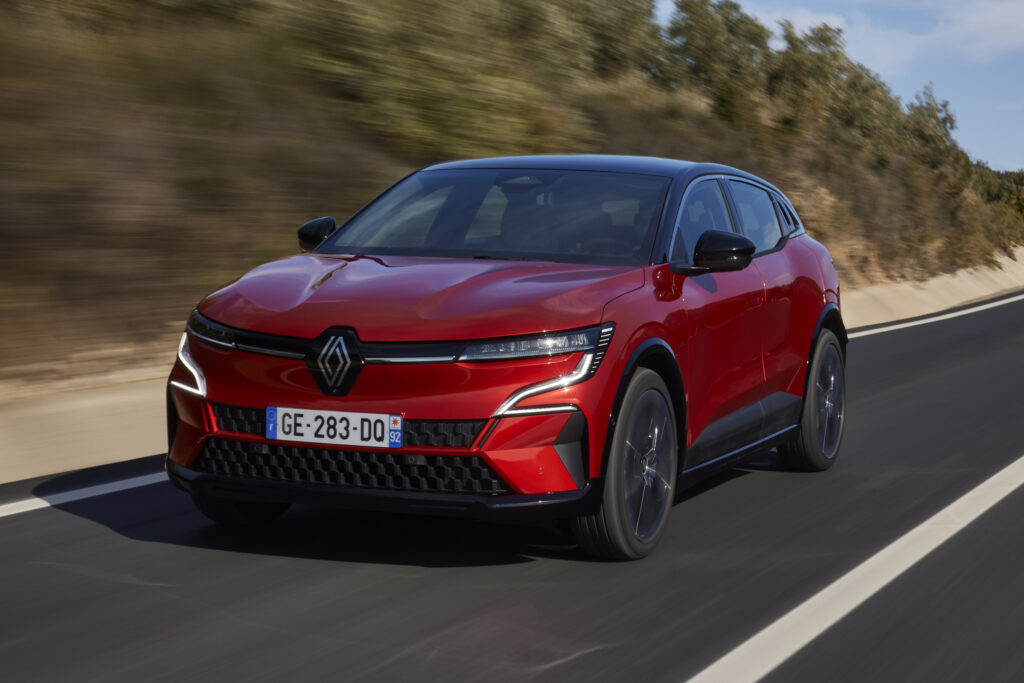
Secția de caroserie și tinichigerie: roboți noi, conexiuni noi
Indiferent de sistemul de propulsie, producția unui vehicul începe în secția de caroserie și tinichigerie. În cazul uzinei de la Douai, procesele de producție din această secție sunt deja automatizate în proporție de 90% prin utilizarea de roboți industriali, iar Renault este în plin proces de trecere completă de la producția lui Scenic la producția lui Megane E-Tech.
Caroseria unui Megane E-Tech este produsă în aproximativ 2 ore și cântărește numai 700 de kilograme cu tot cu portiere și geamuri. Spre deosebire de vehiculele cu motoare termice, portierele lui Megane E-Tech sunt realizate preponderent din aluminiu pentru a contribui astfel la scăderea masei caroseriei, în contextul în care masa unui vehicul electric este influențată semnficativ de bateria Li-Ion.
De altfel, masa totală a vehiculului final este de 1.636 de kilograme în cazul versiunii cu baterie de 60 kWh, cu aproape 200 de kilograme mai mică decât unul dintre concurenții direcți, Volkswagen ID.3, echipat cu o baterie de capacitate similară.
În prezent, uzina de la Douai produce 35 de caroserii pe oră, însă numărul acestora vă crește la 60 de caroserii pe oră după instalarea tuturor noilor roboți adaptați pentru producția lui Megane E-Tech. Așa cum ne explică Anthony Ladirey, reprezentant Renault în cadrul secției de caroserie, în cadrul vizitei, nu este vorba despre o simplă înlocuire a roboților cu unii adaptați pentru Megane E-Tech, ci și de o îmbunătățire a tehnologiei acestora.
Ce este nou la roboții dedicați pentru producția caroseriei lui Megane E-Tech este că aceștia sunt conectați între ei, iar parametri lor pot fi urmăriți în timp real.
Anthony Ladirey, reprezentant Renault la secția de caroserie a uzinei de la Douai
Între timp, roboții înlocuiți care până acum se ocupau de producția caroseriei pentru Scenic vor fi transferați în alte uzine ale Grupului Renault sau vânduți altor companii.
Munca noilor roboți din secția de caroserie este acompaniată de 300 de operatori umani, dintre care 100 asigură suport și mentenanță. De altfel, în atelierul de mentenanță angajații analizează numeroși parametri de funcționare ai uzinei pe mai multe ecrane.
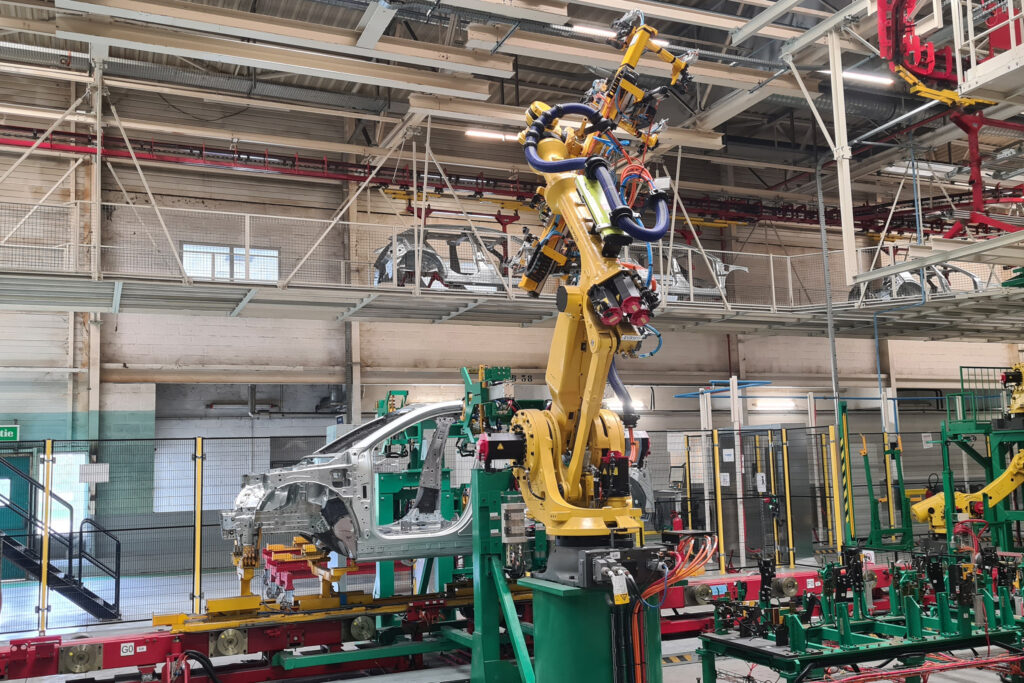
Secția de baterii: training special pentru asamblarea bateriilor
De la secția de caroserii ne mutăm în cea mai nouă secție a uzinei de la Douai, cea în care se asamblează bateriile Litiu-Ion de 40 kW și 60 kW care echipează Megane E-Tech. Aici suntem întâmpinați de Frederic Watremet, șeful secției, care organizează un tur de orizont pentru a ne prezenta toate utilajele utilizate în cadrul procesului.
Practic, ne aflăm într-o zonă care anterior făcea parte din cadrul secției de montaj și care a fost adaptată pentru a permite asamblarea bateriilor Li-Ion. În cadrul procesului de conversie au fost implicați și 30 de angajați din secția de montaj, care au participat la cursuri specifice de electricitate necesare pentru a putea lucra cu platforme de 400 volți, așa cum este și cea a noului Megane E-Tech.
Celulele Li-Ion sunt produse de partenerii sud-coreeni de la LG Chem la o uzină de baterii de 15 GWh din Polonia, iar acestea sunt asamblate de angajați în carcasa de aluminiu a bateriei Li-Ion, amplasată pe un cărucior. Toate componentele necesare sunt depuse în cutii în imediata apropiere a carcasei, iar operațiunile de montare sunt atât manuale, cât și automatizate. În final, cu utilizarea unui echipament de protecție specific, se racordează toate modulele bateriei.
În prezent, secția are o capacitate de asamblare de 30 de baterii pe oră, însă aceasta va fi dublată în cursul anului viitor.
După încheierea procesului de asamblare, bateria trece printr-un test de verificare a conformității elementelor și racordurilor, iar apoi carcasa este închisă. O instalație automatizată montează apoi o garnitură în jurul bateriei și urmează testul de etanșeitate pentru circuitul de răcire și pentru a verifica dacă există zone în care pot pătrunde aerul sau apa.
Frederic Watremet, șef secție montare baterii Li-Ion
Ulterior acestor două teste intermediare are loc și testul final: încărcarea bateriei la una dintre cele 12 stații de încărcare din secție pentru a verifica dacă procesul este corespunzător cu specificațiile. Bateria se încarcă apoi până la capacitatea de 37%, valoare cu care este transportată în secția de montaj.
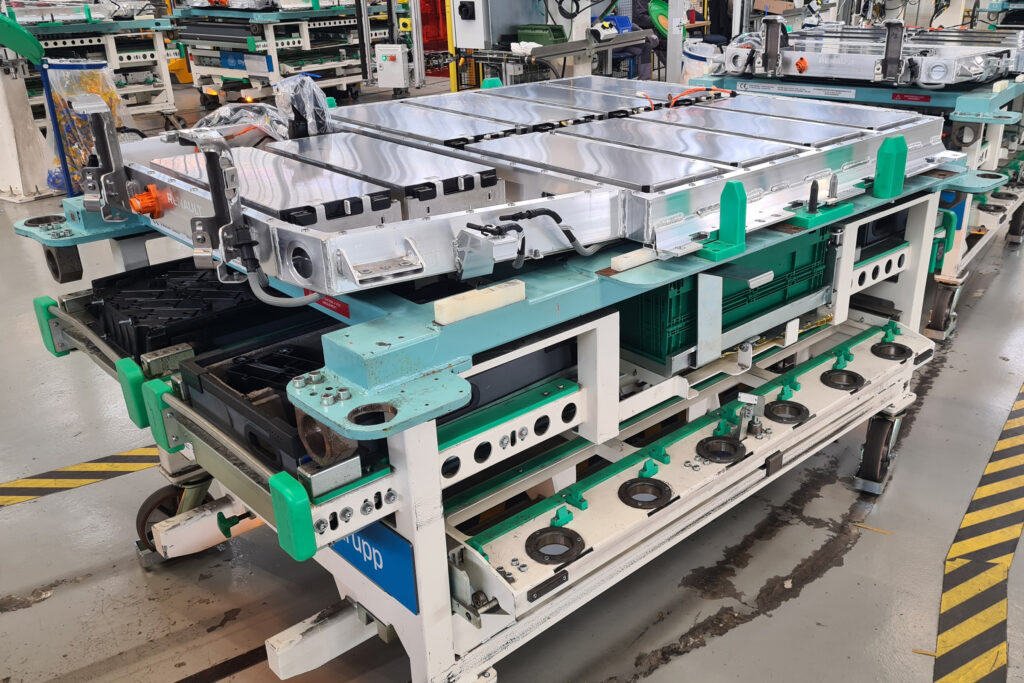
Secția de montaj: Megane E-Tech prinde contur
Rolul de ghid este preluat de Valentin Lartigue, șeful secției de montaj unde lucrează 1.100 de angajați pe 500 de posturi. În prezent, se produc circa 500 de unități Megane E-Tech pe zi, în condițiile în care compacta electrică a primit deja peste 50.000 de comenzi.
Procesul inițial prin care secția de montaj a fost adaptată pentru a produce și vehicule electrice a necesitat șapte săptămâni de muncă pentru instalarea noii linii de asamblare pe care Renault o numește “Alliance Standard Line”, iar aceasta a fost inaugurată în ianuarie 2022 și permite asamblarea simultană de vehicule cu motoare termice și vehicule electrice.
Una dintre noutățile majore este că întregul proces de montaj are acum loc la parter, pe o suprafață totală de 38.000 de metri pătrați, în contextul în care anterior secția avea și un etaj. Practic, au fost înlocuite 100 de mașinării grele și 400 de stații de lucru.
Valentin Lartigue, șef secție montaj la uzina din Douai
O altă noutate comparativ cu epoca “pre-electrică” este că fiecare stație de lucru are acum o platformă mobilă, care poate ridica sau coborî caroseria mașinii între 20 de centimetri și 1,3 metri, ceea ce simplifică munca operatorilor umani în procesul de montare a componentelor și echipamentelor.
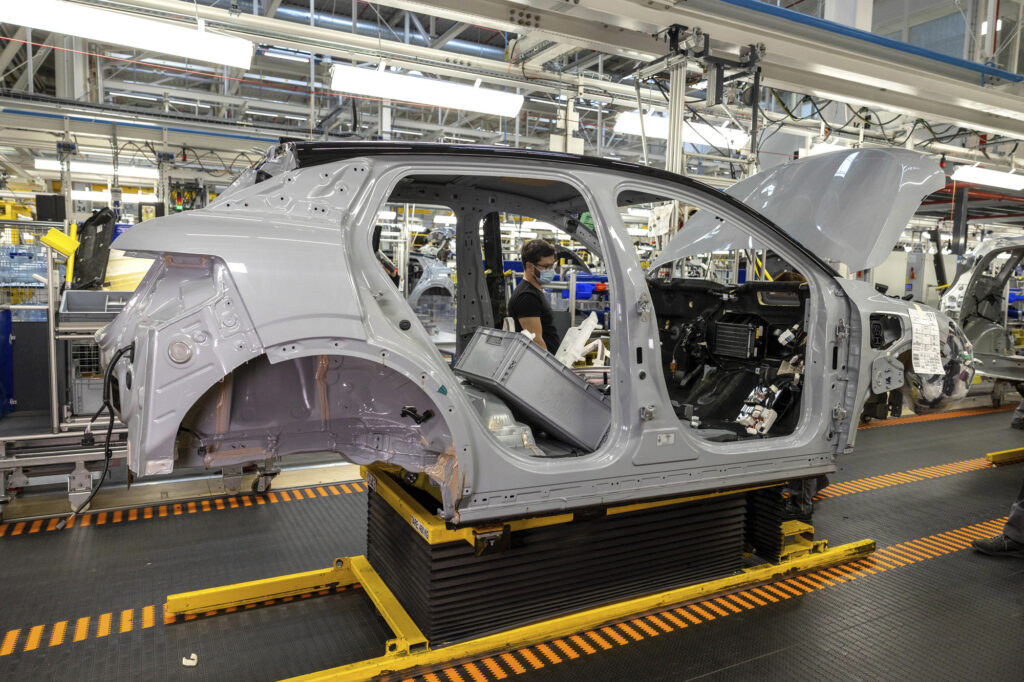
În plus, operatorii umani au la îndemână toate componentele pe care trebuie să le monteze pe caroserie, întrucât Renault a introdus 400 de mici vehicule autonome capabile să transporte echipamente către linia de asamblare. Acestea sunt cunoscute drept AVG, un acronim care provine de la Auto Guided Vehicle.
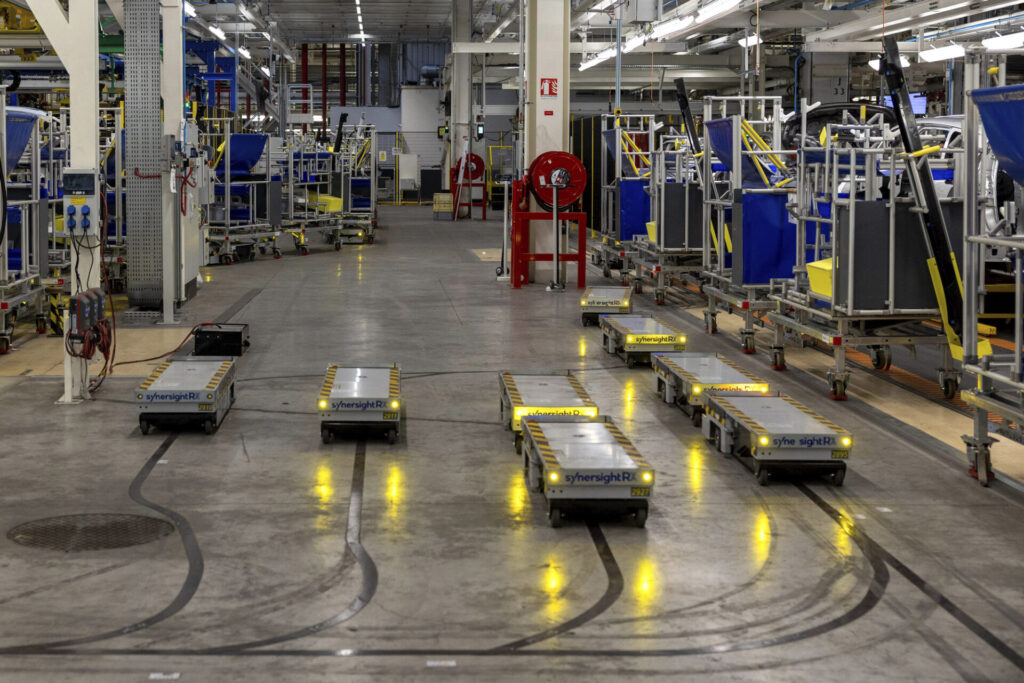
De asemenea, Renault a schimbat și modul în care în care comunică cu furnizorii de componente. Pentru a evita formarea unor stocuri mari de piese, acestea sunt livrate de furnizori în timp real, în funcție de necesitățile specifice fiecărui vehicul în parte, pe baza personalizărilor preferate de clienții finali.
În total, procesul de inginerie pentru asamblarea unui Megane E-Tech durează circa 220 de minute, comparativ cu cele 270 de minute necesare pentru Espace, o scădere generată de faptul că vehiculele electrice au unele proceduri simplificate comparativ cu mașinile cu motoare termice.
În faza finală, vehiculul asamblat primește anvelope și încep numeroase teste pentru identificarea eventualelor probleme: teste la motor, banc de probă cu camere de 360 de grade, tunel de lumină pentru identificarea unor defecte vizuale, test dinamic de accelerație inclusiv pe suprafață denivelată și o cabină de duș pentru verificarea etanșeității.
Rezultatul final este un model electric care i-a surprins plăcut pe jurnaliștii auto din România care au testat compacta timp de 9 zile în vara anului 2022 în cadrul road tripului ROCHARGE organizat de Autocritica, atât în ceea ce privește interiorul modern, cât și în privința performanțelor, autonomiei sau a vitezei de încărcare a bateriei.
În perioada următoare, Megane E-Tech va avea doi prieteni electrici pe liniile de asamblare. Primul va fi versiunea electrică a lui Scenic, pe care Renault nu a prezentat-o încă publicului, dar care va intra în producție de serie peste numai câteva săptămâni.
Ulterior, la sfârșitul acestui an vor fi produse primele unități ale modelului electric de oraș Renault 5, înainte ca producția de serie la nivel industrial să demareze la începutul anului viitor. Recent, constructorul francez a publicat o serie de teasere și informații despre versiunea de serie a lui Renault 5.
Cu noul Renault 5, considerat înlocuitorul actualului Renault Zoe, uzina de la Douai va închide practic cercul, pentru că originalul Renault 5 lansat în 1972 a fost unul dintre primele modele produse în această fabrică.
Uzina din Douai, parte din complexul industrial Renault ElectriCity
Pe baza dezvoltării noilor modele electrice, uzina de la Douai a căpătat o importanță majoră în strategia Grupului Renault, iar aceasta face parte din complexul industrial Renault ElectriCity, anunțat în vara anului 2021. Practic, Renault a integrat cele trei uzine pe care le deține în nordul Franței într-un hub de producție.
Alături de Douai, în această regiune există și uzina de la Maubeuge, construită în 1969, unde se produc în special utilitare precum Renault Kangoo și Renault Kangoo Van E-Tech, dar și utilitare ale partenerilor precum Nissan NV250 și Mercedes-Benz Citan. În plus, tot în această regiune există și uzina de la Ruitz, construită în 1970, unde se produc în special cutii de viteze automate. Între timp, motoarele electrice pentru Megane E-Tech sunt produse la uzina de la Cleon din nord-vestul Franței.
Prin intermediul celor trei uzine integrate în conceptul ElectriCity, Renault își propune să producă 400.000 de vehicule electrice pe an începând din anul 2025.
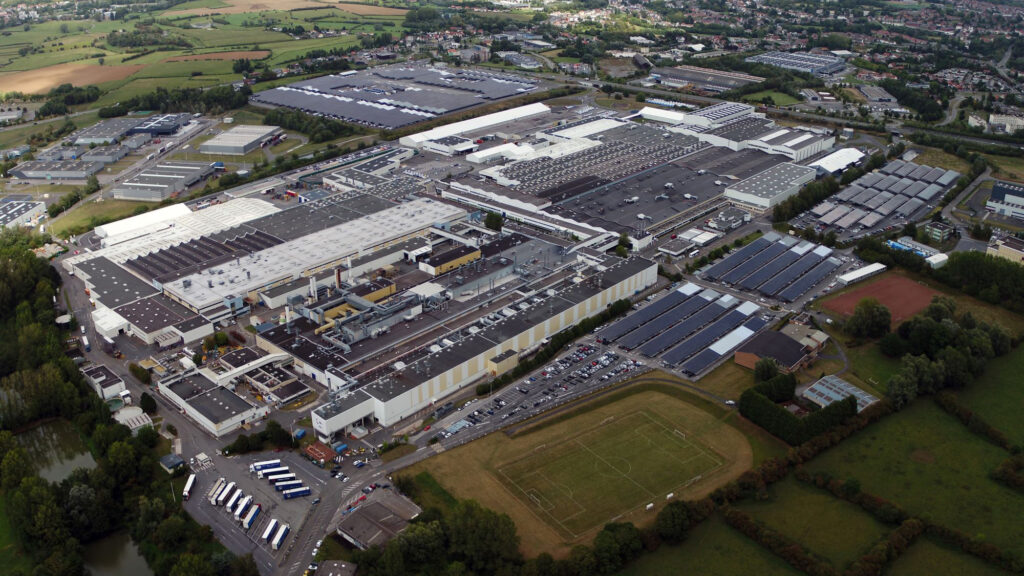
Gigafactory: baterii produse integral în Franța
Pe lângă uzinele din anii ‘70 care au fost modernizate pentru a acomoda producția de vehicule electrice și componente pentru vehicule electrice, Renault se adaptează pentru a produce propriile baterii pentru modele electrice.
La câteva sute de metri de uzina de la Douai, pe un teren cu o suprafață de 50 de hectare, constructorul francez a început în vara anului 2022 construcția unei uzine Gigafactory pentru baterii. Uzina este construită în parteneriat cu producătorul chinez Envision AESC, care va investi în total aproximativ 2 miliarde de euro în acest proiect.
Spre finalul vizitei de la Douai am trecut și pe lângă șantierul acestei uzine, care va avea o capacitate de producție de 9 GWh pe an în 2024 și de 24 GWh pe an în 2030. Bateriile vor fi dezvoltate inclusiv pentru viitorul Renault 5, dar și pentru alte viitoare modele electrice sub brandul Renault.
De asemenea, Grupul Renault va construi o uzină Gigafactory și în Dunkirk, orașul de coastă unde a avut loc celebra Operațiune Dynamo din al doilea Război Mondial, în cadrul căreia 338.000 de soldați ai trupelor Aliate au fost evacuați în Marea Britanie. Acest proiect este derulat împreună cu start-up-ul francez Vektor, la care Renault a cumpărat peste 20% dintre acțiuni.
O analiză realizată de Autocritica în 2022 a scos în evidență că există aproximativ 30 de proiecte în 10 țări europene pentru construcția de uzine pentru baterii, iar cele mai ambițioase programe sunt derulate de Renault, Grupul Volkswagen și Stellantis.
Alternativa la care aspiră Renault: baterii solid-state
Chiar dacă pe hârtie lucrurile arată promițător în perspectiva producției de baterii Li-Ion în Europa pentru vehicule electrice, în practică există numeroase controverse cu privire la abilitățile producătorilor de a se aproviziona cu materiile prime necesare. Cei mai mulți furnizori de materii prime precum litiu, grafit, nichel, mangan și cobalt provin din Asia, America de Sud și Africa, iar Europa are rezerve limitate.
În cadrul vizitei de la Douai, Luciano Biondo, directorul Renault ElectriCity, a evitat să dezvăluie sursele de proveniență pentru materiile prime care vor fi utilizate la producția de baterii la viitoarea uzină Gigafactory de la Douai, însă consideră că industria auto va reuși într-un interval de timp rezonabil să găsească o alternativă în bateriile solid-state.
Nu putem spune de unde vom achiziționa materiile prime, pentru că suntem încă în negocieri, dar trebuie să asigurăm materiile prime pentru toate lanțurile de furnizare. Știm ce înseamnă astăzi o baterie pentru mașini electrice, dar nu știm ce va fi peste 10 ani. Va găsi cineva o idee nouă în termeni de materii prime? Vom avea o baterie solid-state în 10 ani? Este o dilemă pe care o au toți producătorii auto. Fiecare încearcă să aibă propriul departament de cercetare și dezvoltare pentru a descoperi o alternativă la bateriile Li-Ion. Noi ne-am dezolvat planul pe baza a ceea ce reprezintă astăzi o baterie și de aceea construim două uzine pentru baterii, dar lucrurile se pot schimba.
Luciano Biondo, directorul Renault ElectriCity
Bateriile solid-state reprezintă cea mai promițătoare tehnologie nouă pentru mașinile electrice. În principiu, celulele unei baterii solid-state folosesc aceeași reacție chimică pentru ionii de litiu ca și celulele bateriilor Li-Ion, însă diferența majoră este utilizarea unui electrolit solid în defavoarea unui electrolit lichid.
Teoretic, bateriile solid-state se încarcă în 10 minute și oferă autonomii de peste 800 de kilometri, însă acestea își păstrează proprietățile pentru numai aproximativ 100 de cicluri de încărcare-descărcare.
Până la apariția pe piață a unei baterii solid-state care să aibă un număr decent de cicluri de încărcare, bateriile Li-Ion rămân singura opțiune realistă pentru constructorii auto și, implicit, pentru Renault. Și asta este valabil indiferent că vorbim despre Megane E-Tech, aflat deja în plină producție, sau de versiunea de serie a modelului de oraș Renault 5, care va ajunge pe linia de asamblare peste numai câteva luni.
La Douai, nu la Dubai, așa cum îi place directorului Luciano Biondo să glumească.