La nivel global, industria auto este unul dintre principalii clienți ai producătorilor de oțel. În Europa, 17% din consumul total de oțel al Uniunii Europene din anul 2022 a ajuns la producătorii de mașini, procent în care sunt luate în considerare atât producția internă de oțel a Uniunii, cât și importul de oțel din afara blocului comunitar. Astfel, singurul sector care a consumat mai mult oțel în Europa a fost cel al construcțiilor (37%), potrivit datelor publicate în raportul European Steel in Figures publicate de Asociația Producătorilor de Oțel din Europa.
Pe de altă parte, industria auto are nevoie de un oțel cu duritate și siguranță mai mari decât oțelul din domeniul construcțiilor pentru a respecta reglementările europene în domeniu. Din acest motiv, oțelul produs pentru industria auto este mai scump comparativ cu cel folosit în construcții, astfel că industria auto este un client semnificativ pentru producătorii de oțel.
Cu PPC Blue, fiecare încărcare devine parte dintr-o călătorie mai smart. Noi aducem mobilitatea electrică mai aproape de tine, fie că ești acasă, la birou sau în deplasare. Tu trebuie doar să te bucuri de libertatea de a merge mai departe, fără griji. Fiecare încărcare înseamnă un pas spre un viitor care contează.
Găsește stația de încărcare potrivită pentru tine pe ppcblue.ro
Impactul producției de oțel asupra mediului
La nivel global, producția de oțel este responsabilă pentru aproximativ 7% din emisiile totale de dioxid de carbon, iar procentul este ușor mai scăzut în Uniunea Europeană: 5%. Pe de altă parte, 30% dintre emisiile de dioxid de carbon ale industriei germane provin de la furnalele în care se produce oțel.
Motivul pentru care oțelul are o contribuție atât de mare la emisiile industriale este simplu: la nivel global, oțelul are o largă utilizare în numeroase domenii de activitate, de la construcții și infrastructură până la industria auto.
Aproximativ 75% din cantitatea totală de oțel se produce printr-o metodă numită Blast Furnace – Basic Oxygen Furnace (BF-BOF), care implică topirea minereului de fier la temperaturi de circa 1.700 de grade Celsius în prezența oxigenului din aer și a cocsului. Cocsul este un tip de combustibil solid și poros obținut prin încălzirea cărbunelui la temperaturi ridicate, iar în urma acestui proces se generează căldură și monoxid de carbon.
Ulterior, monoxidul de carbon reacționează cu minereul de fier și produce dioxid de carbon (care este evacuat în atmosferă) și fier topit, care ulterior se transformă în oțel printr-o serie de procese suplimentare.
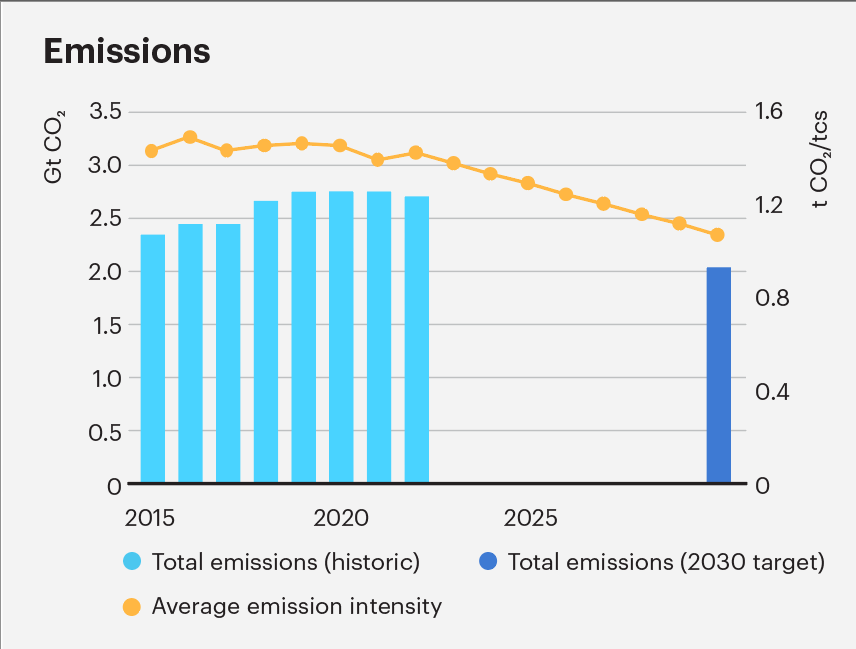
O altă metodă de producție este Electric Arc Furnace (EAF), care în principiu presupune reciclarea oțelului deja folosit, motiv pentru care această metodă este mai puțin poluantă pentru mediul înconjurător. Altfel, în prezent, aceasta este cea mai eficientă metodă de producție din punct de vedere al costurilor și al gradului de reducere a emisiilor de dioxid de carbon: comparativ cu metoda BF-BOF, reducerea emisiilor variază între 35% și 65%, în funcție de calitatea oțelului reciclat și de alți parametri.
Cu toate acestea, utilizarea acestei metode este îngreunată de faptul că în forma sa finită oțelul integrează și alte metale poluante dificil de separat, în funcție de industria în care va fi utilizat.
De altfel, reciclarea oțelului pentru industria auto este în prezent la niveluri relativ reduse. Printre constructorii auto care folosesc oțel reciclat în procesul de producție se numără Volvo (15% din cantitatea totală), Renault (17%), BMW (25%) sau Stellantis (30%).
Una dintre explicațiile pentru care acest procent nu este mai ridicat este că oțelul reciclat în Uniunea Europeană are în mare parte un conținut de cupru de 0,2 – 0,25%, în timp ce industria auto are nevoie de oțel cu o compoziție de cupru de cel mult 0,06%.
Pe de altă parte, specialiștii propun ca producătorii de mașini să regândească designul caroseriei pentru ca oțelul integrat să fie mai ușor de recuperat la finalul utilizării mașinii respective. Acest lucru se poate rezolva atât prin introducerea unor procedee specifice pentru demontarea componentelor și separarea metalelor, cât și prin gândirea unui proces complex de colectare a oțelului la finalul duratei de viață a mașinii.
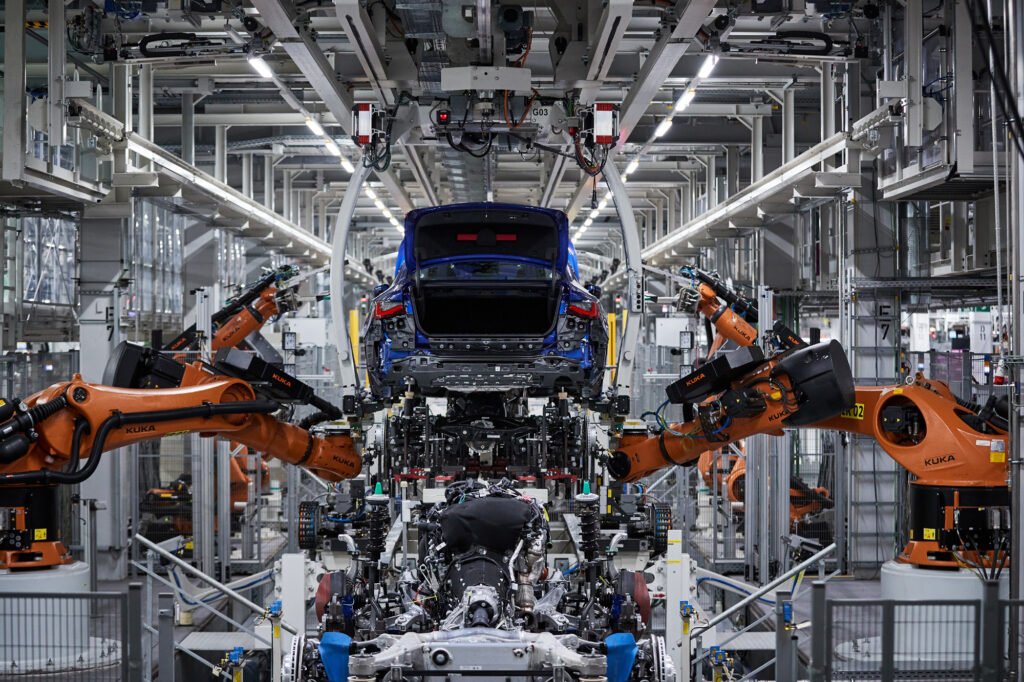
Tehnologii moderne pentru oțel verde
Ca urmare a Acordului de la Paris privind schimbările climatice și ambiția Uniunii Europene de a deveni neutră din punct de vedere al emisiilor de dioxid de carbon până în 2050, specialiștii din industrie au elaborat o serie de metode alternative pentru reducerea emisiilor în cadrul procesului de producție al oțelului.
În cazul în care producția oțelului prin aceste metode alternative are loc fără emisii, produsul finit rezultat este cunoscut în industrie drept oțel verde. În prezent, singura modalitate cunoscută pentru a produce oțel verde este utilizarea hidrogenului verde.
Metodele în sine nu sunt revoluționare și se pot aplica teoretic în numeroase alte domenii industriale, însă cel puțin pentru moment acestea sunt dificil de implementat, în special din punct de vedere al costurilor sau al eficienței energetice.
Una dintre idei pleacă de la prima etapă de producție, și anume eliminarea oxigenului din minereul de fier. Astfel, în loc de utilizarea cocsului, producătorii pot folosi gaze naturale, care au emisii mai scăzute, însă cea mai eficientă metodă ar fi, teoretic, utilizarea hidrogenului.
Cu toate acestea, tehnologiile disponibile pentru a produce hidrogenul necesar unei astfel de metode sunt poluante sau scumpe. În prezent, 95% din cantitatea totală de hidrogen produsă industrial la nivel global este generată prin două metode:
- reformarea gazului natural: gazele naturale sunt amestecate cu un abur fierbinte, proces din care rezultă hidrogen, dar și gaze nocive precum monoxid de carbon și dioxid de carbon
- gazificarea cărbunelui: utilizarea de cărbuni într-un recipient sub presiune în care există oxigen și abur fierbinte, proces în urma căruia rezultă un gaz care conține hidrogen și monoxid de carbon.
Întrucât acest tip de hidrogen este produs cu emisii de dioxid de carbon, specialiștii îl numesc frecvent hidrogen gri.
Există o tehnologie care permite obținerea hidrogenului fără emisii de dioxid de carbon: electroliza apei. Totuși, acest lucru presupune utilizarea unei mari cantități de energie electrică, iar aceasta ar trebui să provină din surse regenerabile pentru ca oțelul rezultat la final să aibă emisii cât mai reduse. În plus, parțial din cauza cantității mari de energie electrică necesară, producția de hidrogen prin electroliza apei este scumpă și, implicit, ineficientă în prezent din punct de vedere al costurilor de producție. Hidrogenul obținut prin această metodă se numește hidrogen verde.
De altfel, potrivit datelor din raportul Case Study Germany: Green steel production and demand in the automotive industry, mai mulți producători de oțel au primit subvenții de stat de miliarde de euro pentru a produce oțel cu hidrogen verde, însă ulterior au amânat sau chiar anulat implementarea proiectelor din cauza îngrijorărilor că acestea sunt insuficiente pentru a acoperi costurile actuale de producție ale hidrogenului verde.
O metodă de compromis pentru producția de hidrogen accesibil din punct de vedere al costurilor și cu emisii scăzute presupune utilizarea unor metode de reformare a gazelor naturale sau de gazificarea cărbunelui în combinație cu un sistem de captare și stocare a dioxidului de carbon care rezultă în urma procesului de producție, tehnologie cunoscută drept Carbon Capture and Storage (CCS). În acest caz vorbim despre ceea ce specialiștii numesc hidrogen albastru și este tipul de hidrogen cel mai frecvent întâlnit în prezent la stațiile de încărcare pentru mașini electrice alimentate cu hidrogen precum Toyota Mirai sau Hyundai Nexo.
De altfel, tehnologia CCS a fost promovată insistent de marii producători de petrol la Conferința COP 28, care a avut loc în decembrie 2023 în Dubai. Totuși, această tehnologie nu este suficientă pentru a avea un impact real asupra emisiilor de dioxid de carbon. De exemplu, proiectele operaționale de captare a dioxidului de carbon au o capacitate de captare de circa 49 de milioane de tone pe an, ceea ce reprezintă doar 0,13% din cantitatea de dioxid de carbon emisă anul trecut de industriile energetice.
Mai puțin oțel, mai mult aluminiu
O metodă complementară pe care constructorii auto o pot aplica pentru a reduce emisiile generate în timpul producției este și scăderea masei unui autovehicul prin înlocuirea parțială a oțelului cu aluminiu.
Ideea de bază este ca producătorii să utilizeze oțel cu rezistență mai mare pentru a reduce astfel cantitatea totală necesară, caz în care o serie de studii arată că masa unui vehicul ar putea fi redusă cu 2% – 6%. În plus, masa caroseriei în sine poate fi redusă cu până la 35% în cazul înlocuirii parțiale a oțelului cu aluminiul.
Pe de altă parte, masa medie a unui vehicul comercializat în Europa a ajuns în 2022 la 1.518 kilograme, cu 19% peste masa medie raportată pentru anul 2001, în special ca urmare a creșterii vânzărilor de SUV-uri, care aveau o cotă de piață de 51% în 2023.
Cu cât s-ar scumpi mașinile daca s-ar folosi oțel verde?
Grupul Ricardo, care dezvoltă soluții sustenabile pe baza unor proiecte realizate de ingineri, cercetători și consultanți financiari, a realizat un studiu cu privire la impactul teoretic al utilizării oțelului verde în prețul final al unei mașini.
Autorii au plecat de la ipoteza că pe parcursul timpului costurile de producție pentru hidrogenul verde ar scădea de la valorile actuale până la praguri semnificativ mai mici și că aproximativ 50% din producția de oțel a anului 2030 va fi realizată prin metode cu emisii foarte scăzute, cu o creștere la 88% în 2035. Într-un astfel de scenariu, o mașină produsă în 2030 cu oțel verde va costa cu numai 43 de euro mai mult decât aceeași mașină produsă cu oțel obținut prin cea mai poluantă metodă. În plus, costul suplimentar ar urma să scadă la numai 8 euro pe mașină până în anul 2050.
În același timp, autorii susțin că, dacă producătorii ar utiliza exclusiv oțel verde în 2030, atunci prețul unei mașini ar crește cu numai 105 euro comparativ cu scenariul în care se folosește oțel generat prin metode tradiționale.
Primul producător 100% de oțel verde: H2 Green Steel
În perioadele în care tehnologiile moderne pătrund timid pe piață, așa cum este și cazul oțelului verde, cel mai mare avantaj îl au noile companii, întrucât acestea pot dezvolta facilități de producție de la zero adaptate direct la noile condiții tehnice.
Așa a apărut, în 2021, start-up-ul suedez H2 Green Steel, care a accesat mai multe runde de finanțare cu ajutorul cărora își propune să construiască în regiunea Boden-Luleå din nordul Suediei o uzină de oțel verde care va integra și o uzină de hidrogen verde. Producția de oțel este programată să înceapă în 2025 și să ajungă la o capacitate de 5 milioane de tone de oțel anual cel târziu în 2030. Principalul investitor este Vargas, care în același timp este unul dintre principalii acționari la Northvolt, un start-up suedez de baterii pentru mașini electrice, iar compania este condusă de Henrik Henriksson, fost CEO la Scania.
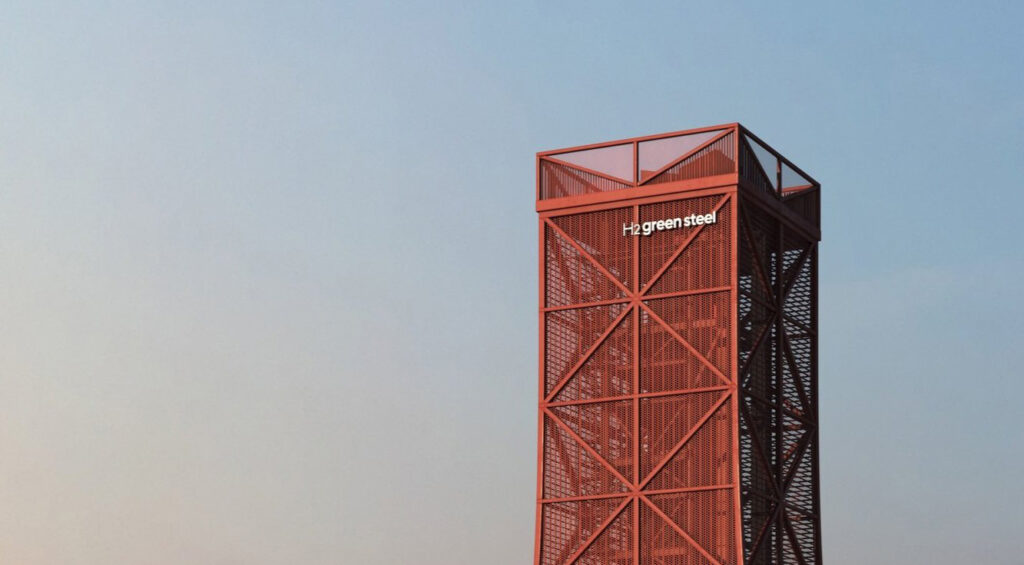
H2 Green Steel a anunțat deja semnarea mai multor parteneriate cu constructori auto, printre care Grupul BMW, Mercedes-Benz (50.000 de tone de oțel verde anual), Volvo (începând din 2026) sau Porsche (35.000 de tone de oțel verde anual), pe lângă semnarea unui parteneriat cu compania de regenerabile Iberdrola pentru construcția unei uzine de hidrogen de 1 GW în Peninsula Iberică.
H2 Green Steel estimează că oțelul verde pe care îl va produce în Suedia va fi cu 20% – 30% mai scump decât oțelul convențional, ceea ce înseamnă o creștere a prețului mediu final al unei mașini cu 100 – 200 de euro, ușor mai consistentă comparativ cu datele prezentate în studiul Grupului Ricardo.
În ciuda optimismului arătat de studii și de ambițiile start-up-ului H2 Green Steel, Agenția Internațională de Energie atrage atenția într-un amplu raport dedicat pieței globale a oțelului că tranziția spre oțelul verde se anunță una mult mai lentă.
„În prezent se produc mai puțin de un milion de tone de oțel cu emisii scăzute, iar sectorul oțelului nu își îndeplinește obiectivele pentru a atinge neutralitatea climatică până în 2050. În plus, sunt anticipate apariția unui număr semnificativ de uzine de oțel tradiționale, cu capacități de producție planificate sau în construcție de 90 de milioane de tone de oțel până în 2025.”
Foto principală: Dreamstime.